The Egan Report “Rethinking Construction” published in July 1998 by the Construction Task Force, has concluded that UK construction is in need to concentrate towards a more efficient and improved output quality. The construction industry is to focus on improving client’s satisfaction. This can be done by cutting the construction costs, increased in quality of construction, and moving towards sustainable construction with emphasis on prefabrication and off-site assembly. As being cited in the DTI report (prepared by Phillipson, 2001), The Egan Report also suggested that the construction industry is in need to become more innovative to streamline the construction process and to develop partnering between contractors and suppliers in moving towards a dispute free industry.
Since the publication of the Egan Report, prefabrication has then been identified as a major way forward in delivering these required improvements (Phillipson, 2001). Major impact caused by the Egan Report has included a range of initiatives such as Movement for Innovation (M41) and the Construction Best Practice Programme.
Currently, the UK construction industry is applying prefabrication to a wide variety of forms and applications. This ranges from the simple prefabricated site hut, which has been a long established application, up to volumetric units that can be delivered to site to integrate into the structure of the building.
At the beginning of the 21st century, UK has been predicted in need for about four million and 225 thousand new homes by 2016 (DETR 1998a, Cavill 1999). The issues include increasing the current density of housing developments from 30 houses to 50 houses per hectare, curbing carbon dioxide emissions from water and space heating without eliminating a comfortable internal temperature in the particular house, reducing the destruction of Greenfield land and building sustainable houses which allow the occupants to feel part of a community (DETR 1999, DETR 1998b).
This concern has lead to DETR producing a Housing Green Paper “Quality and Choice: A Decent Home for All” in April 2001 which identified prefabrication as a way forward in providing affordable housing, and have considered ways in which more resources could be used in schemes that use prefabrication.
Modularisation or modular design has been described as the key to prefabrication (Loetterle, 2004). Modular design refers to construction using standardised units or standardised dimensions. Modular buildings do not have to be built using prefabrication techniques, but they are usually involved.
Thursday, November 04, 2004
Friday, October 29, 2004
It's a PhD, not a Nobel Prize - Mullins, G (2002), Studies in Higher Education Volume 27, No.4, p.386, Carfax Publishing
' A PhD is a stepping stone into a research career. All you need to do is to demonstrate your capacity for independent, critical thinking. That's all you need to do. A PhD is three years of solid work, not a Nobel Prize' (Maths-Eng/Female/18)
Tuesday, October 19, 2004
Review of Willowater, UK
Below is a very interesting website I've encountered during my literature review:
www.homeforlife.co.uk
This link has brought me into a mobile prototype building concept being conceived by John Talbot based on Roger Dean's architectural idea. This prototype building is constructed for The Bishops Wood Centre in Worcester using a new modular building method and designed to be in harmony with the natural environment.
www.homeforlife.co.uk
This link has brought me into a mobile prototype building concept being conceived by John Talbot based on Roger Dean's architectural idea. This prototype building is constructed for The Bishops Wood Centre in Worcester using a new modular building method and designed to be in harmony with the natural environment.

In terms of its building services requirement, underfloor heating (with provision for open fires and log burners), air flow management system, air conditioning and smart house technology is to be installed on site.
The off-site construction start from the inside with the inner room shell's to be made of fibrous plaster and switches to be built into the shells. The modules will then be transported to the site and secured together. Next step is to have a raft of concrete cement applied to the structure and insulation sprayed to the internal walls of the shells. As mentioned earlier, wiring power plugs and other services are mainly underfloor and installed on site.
This prototype earthship modular building aimed to save about 10-20% on materials and a further of 40-50% on labour. Savings than utilised for fitting out a high quality interior and toxin free materials.
Earthships buildings always known as having the advantage of being less susceptible to the impact of extreme outdoor air temperatures, hence building users wouldn't feel the effects of adverse weather as much as in a conventional buildings. This resulting in temperatures inside the buildings that are more stable with less temperature variability, and interior rooms that seem more comfortable.

Another good point to be added is the use of modular construction that not only help balancing the time cost and quality, but also in terms of creating a better working environment in the factory. Modular construction also aid to mitigate working on site that can sometimes be hazardous.
One thing I'm in doubt about: looking at the 3D view of the building, wouldn't it be difficult to hang anything on the wall as there are hardly any flat areas around the shells? How maintenance can be carried out since the services will be built underground? Wouldn't it going to be expensive to dig the flooring up?
Other downside that need to be taken into account for having an earthships construction is the level of care required to avoid moisture problems, during both the construction and the life of the building.
It will be quite interesting to actually find out the possibility of using wood construction for the shells. Could it be cheaper and better in terms of waste management at the end of the building's life time?
Friday, October 15, 2004
Japanese prefabrication housing construction
As stated by CIRIA Special Publication 139, Japanese house building market is substantially larger than that of the UK and new build housing output in Japan has varied between 4.5 to 8 times larger than in the UK.
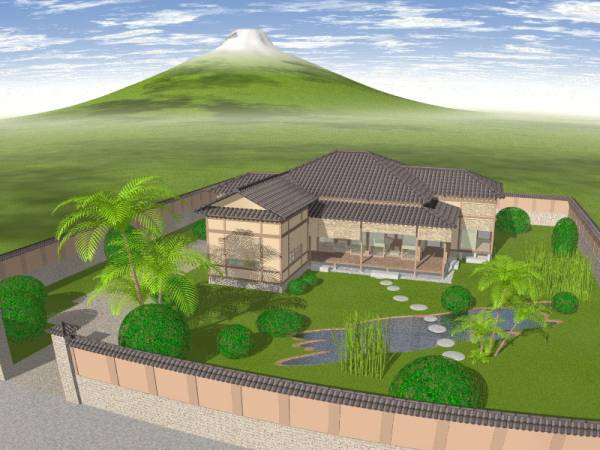
Japanese traditional timber housing was constructed using post-and-beam timber frame methods. Modernism then had started in Meiji Period (1868-1912) which gave flexibility to internal layouts and allowed occupants to perceive internal dimension and horizontal spaces from any position within their houses in a more fluid manner than in Western Style dwellings.
For its timber-frame dwellings, Japanese has used a method of 'Precut' which consists of timber structural ridig frames, with members cut to size and finished with complex connections in factories that based on traditional jointing methods.
The principal assumption of an off-site construction/mass production is that reduction in the variety of components used in a system will allow economies in the production of components. The unit cost is reduced by mass production, on assembly lines, where fixed costs (e.g. investment in factory plant) are spread over an increasing number of identical components. Variable costs (e.g. cost of material) are roughly constant per unit, although there may also be benefits because of large volume purchase (CIRIA, 1996).

Modular construction aims to achieve a predictable and efficient construction with excellent quality as promised. It is hoped to give a lower whole life cost, better working environment in the factory, and to achieve a minimum on-site time.
Nevertheless, downside might occur when an off-site construction is in need of larger capacity transport vehicle than in-situ constructed project. Cost also can be appear to be higher than anticipated due to craneage limitation.
So, how sustainable a modular construction can be?
Thursday, October 14, 2004
Housing in the UK - towards sustainability
During my literature review, I had found out that housing markets in the UK have undergone major structural change over the last 20 years which includes the shift from public to private housing provision.
In this matter, 80% of new housing has been built to satisfied the private individuals and only the other 20% goes to housing association, with the figure being confirmed by CIRIA in their Special Publication 139. Proportion of owner-occupied housing has also risen to nearly 70% of all housing, followed by the change in household formation pattern along with the demographic transformation such as a growing number of single parents, elderly, and disabled people required special need housing.
Environmental awareness has also play an important role in the last 20years. There is an increasing need to reduce the pollution and to limit the waste in production through recycling. This followed by the need for longevity of housing because of the ageing housing stock and low replacement rate.
CIRIA also stated that new demands for low energy housing may means that the use of seemingly robust technologies such as bricks could be stretched beyond their physical limits in terms of embodied energy, buildability, and thermal performance in use. An increasing number of housing project involve the need to innovate, unfortunately, as stated in IPRA (1992), UK house builders invest almost nothing in research and development!
In this matter, 80% of new housing has been built to satisfied the private individuals and only the other 20% goes to housing association, with the figure being confirmed by CIRIA in their Special Publication 139. Proportion of owner-occupied housing has also risen to nearly 70% of all housing, followed by the change in household formation pattern along with the demographic transformation such as a growing number of single parents, elderly, and disabled people required special need housing.
Environmental awareness has also play an important role in the last 20years. There is an increasing need to reduce the pollution and to limit the waste in production through recycling. This followed by the need for longevity of housing because of the ageing housing stock and low replacement rate.
CIRIA also stated that new demands for low energy housing may means that the use of seemingly robust technologies such as bricks could be stretched beyond their physical limits in terms of embodied energy, buildability, and thermal performance in use. An increasing number of housing project involve the need to innovate, unfortunately, as stated in IPRA (1992), UK house builders invest almost nothing in research and development!
Friday, September 10, 2004
sustainable housing
I do believe that people now and in the future is looking for not only houses or dwellings that are cheap and fast to be built but it must also 'house' a convenient environment and energy efficient that lead to a better low energy affordable houses that can be practised not only in UK but also in other countries that are still under development such as Malaysia and Indonesia.
One thing for sure, cheap and fast built housing can be built using a modular construction (also known as construction using off-site or pre-assembly production). But how energy efficient this can be? What makes it better than a usual on site construction?
Energy efficient dwellings means low energy houses that can be operate and constructed not only using 'green - recyclable' power (such as wind, water and solar/sun) but also by using local materials. Low energy construction also aims in reducing the risks of health and safety if the houses to be built on a brownfield site.
In the mean time, I've been reading some articles as background reading for the past one week so that at least I ve got an idea on what had been contributed to the research knowledge in terms of sustainable housing and had encountered this useful website recommended by my personal tutor: www.greenclips.com
As stated before, one key point for sustainable housing is to built it using a recyclable and (preferably) local material. The construction specifier had published one of their brief papers in greenclips, stated that while the lifecycle data on the environmental performance of metals used in cosntruction is difficult to come by, stainless steel, in fact, does have a recycling rates for architectural products which is very high even after a long service life.
It has stated that in 2002, the International Stainless Steel Forum had estimated the typical recycled content was about 60 percent! Stainless steel also known as a material able to be 100 percent recycled with no downcycling, regardless of how many times it has been previously recycled.
So..will there be a good future for stainless steel in the world of modular construction framework? a task that i should definitely try to find out in my MPhil/PhD research study:)
One thing for sure, cheap and fast built housing can be built using a modular construction (also known as construction using off-site or pre-assembly production). But how energy efficient this can be? What makes it better than a usual on site construction?
Energy efficient dwellings means low energy houses that can be operate and constructed not only using 'green - recyclable' power (such as wind, water and solar/sun) but also by using local materials. Low energy construction also aims in reducing the risks of health and safety if the houses to be built on a brownfield site.
In the mean time, I've been reading some articles as background reading for the past one week so that at least I ve got an idea on what had been contributed to the research knowledge in terms of sustainable housing and had encountered this useful website recommended by my personal tutor: www.greenclips.com
As stated before, one key point for sustainable housing is to built it using a recyclable and (preferably) local material. The construction specifier had published one of their brief papers in greenclips, stated that while the lifecycle data on the environmental performance of metals used in cosntruction is difficult to come by, stainless steel, in fact, does have a recycling rates for architectural products which is very high even after a long service life.
It has stated that in 2002, the International Stainless Steel Forum had estimated the typical recycled content was about 60 percent! Stainless steel also known as a material able to be 100 percent recycled with no downcycling, regardless of how many times it has been previously recycled.
So..will there be a good future for stainless steel in the world of modular construction framework? a task that i should definitely try to find out in my MPhil/PhD research study:)
blank white paper..
Hiya..
And..erm..am not too sure what to write..
you see..my boyfriend had introduced me to blogging but..to tell you the truth I ve never good at writing..;(
So here it is my first blogging..
er..let's start with my brief background..
I am doing my MPhil/PhD in Sustainable Housing area and am just starting last week so..am still in the state of settling down, basically.
I've just realised that MPhil/PhD is quite a lonely experience. But dont get me wrong..that doesnt mean I dont like the experience, in fact, it's actually adding professionalism and discipline into myself!
So..i guess this will be my first blog on a pure blank white paper..;P
And..erm..am not too sure what to write..
you see..my boyfriend had introduced me to blogging but..to tell you the truth I ve never good at writing..;(
So here it is my first blogging..
er..let's start with my brief background..
I am doing my MPhil/PhD in Sustainable Housing area and am just starting last week so..am still in the state of settling down, basically.
I've just realised that MPhil/PhD is quite a lonely experience. But dont get me wrong..that doesnt mean I dont like the experience, in fact, it's actually adding professionalism and discipline into myself!
So..i guess this will be my first blog on a pure blank white paper..;P
Subscribe to:
Posts (Atom)